Solder
Paste: The
properties of a solder paste depend in part
on the metal content, the solder alloy and the solder powder
particle size range. In general terms, increasing metal content
reduces the tendency to slump and reduces the tack life of the
solder paste while the solder balling performance improves.
Typical properties of selected Multicore MP100 solder pastes
are as follows. Full details of test methods will be supplied on
request.
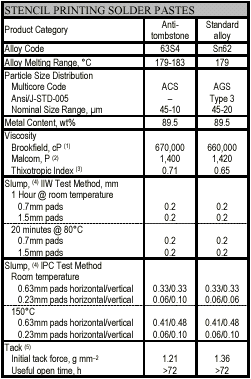
(1)
Measured
at 25°C, TF spindle at 5rpm after 2 minutes.
(2)
Measured
at 25°C and a shear rate of 6s-1
(3)
The
Thixotropic Index (TI) is defined as:
TI=log
(viscosity at 1.8s-1/viscosity at 18s-1)
(4)
The
slump data are expressed as the minimum spacing between pads of
the
size shown that does not allow bridging.
(5)
Tack
data are derived from comparative laboratory tests and do not
necessarily
relate directly to particular user conditions.
PACKAGING
Containers:
Multicore
MP100 solder pastes are supplied in:
1 kg, 500g or 250g plastic jars with an insert to seal
off the surface of the paste
1 kg, 650g or 500g vacuum filled cartridges for direct
application
750g Proflow cassettes
Other forms of packaging may be available on request.
|
|
Shelf
Life: Providing
Multicore MP100 solder pastes are
stored at 5-10°C tightly sealed in the original container, a
minimum shelf life of 6 months can be expected. Air shipment
is recommended to minimise the time the containers are
exposed to higher temperatures.
Multicore MP100 solder pastes have been formulated to
reduce separation on storage to a minimum but should it
occur, gentle stirring for 15 seconds will return the products to
their correct rheological performance.
HEALTH
& SAFETY
WARNING:
The following information is for guidance only and
users must refer to the Material Safety Data Sheet relevant to
specific Multicore MP100 solder paste products before use.
Fumes,
Vapours and Precautions: The
flux fumes given off
at soldering temperatures are irritating to the nose, throat and
respiratory organs. Prolonged or repeated exposure to the
fumes may cause sensitisation.
These materials should always be used in a well ventilated
area and suitable fume extraction should be used to extract
flux fumes away from the operators.
Protection
and Hygiene: Suitable
protective clothing should
be worn to prevent materials from coming into contact with the
skin and eyes. If the materials come into contact with the skin,
the affected area should be cleaned with a proprietary hand
cleanser followed by washing with soap and water. If the
materials come into contact with the eyes, they should be
irrigated thoroughly with running water for at least 10 minutes
and medical attention sought.
Eating, drinking or smoking should not be permitted in the
working area and hands should be washed thoroughly with
soap and warm water before eating.
Fire
Hazards and Precautions: The
flashpoint of the solvent
used in these materials is high (118°C) but it is combustible.
Carbon dioxide, foam or dry powder extinguishers are suitable.
High temperatures may produce heavy metal dust, fumes
and/or vapours. Do not use water where molten metal is
present.
Spillage
and Waste Disposal: Spills
of the materials should
be
scraped up and the contaminated area washed with water. Waste
materials should be stored in closed containers and disposed
of in accordance with the relevant local and national regulations.
|